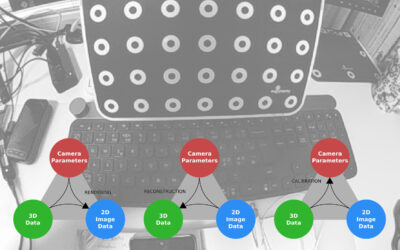
Unveiling the Magic Behind Augumenta’s AR accuracy: Camera Calibration in Smartglasses
Introducing camera calibration and its importance in high-accuracy augmented reality
How to keep your maintenance personnel effortlessly up-to-date and at the same time provide your service customers with added value: Case Nextek & Augumenta SmartAlert
Nextek, a major HVAC system provider in Taipei, Taiwan stands at the forefront of digital transformation by adopting AR and smartglasses into their operations and as a value-adding part of their service to customers. The company uses Augumenta SmartAlert solution to keep maintenance personnel informed about real-time data of HVAC equipment and system status. Nextek also ensures efficient remote support for workers in the field via deploying live video call features as part of the solution. In the first deployment project, the system is taken into use in Victor Taichung’s ultramodern new factory with Nextek’s latest HVAC technology in their facilities.
Nextek designs, installs, and maintains large and complex HVAC systems for industrial facilities and office campuses in Taiwan. The company specialises in energy efficiency and clean-room solutions for example for the Taiwanese high-tech manufacturing industry and medical facilities.
A modern HVAC system produces a flood of data drawn from the system itself, the environment, and the functionality of single pieces of equipment. Traditionally the data, if collected to a BAS system, has been monitored out of control room displays. The maintenance personnel working across the vast facilities with the HVAC equipment has lacked easy access to the real-time data out in the field. When there’s usually only one person in charge of the facility, repeated visits back to the control room to check values and again to the equipment to make adjustments takes unnecessary time and effort. All of this delays the actual work and problem-solving.
We worked together with Nextek to outline a solution on how to make the data usable no matter where or when a worker needs the information. We opted to go for our SmartAlert solution which runs on smartglasses and mobile devices. Based on the input received from Nextek experts in brainstorming sessions, we added our own unique marker technology and live video call features for additional support. In this case, the best match were lightweight smartglasses as the medium for data. Glasses leave the hands of the maintenance worker free to work on the equipment and any notifications reach the end-user immediately as it’s displayed right in-front-of their eyes.
We built support for Nextek’s maintenance information systems and the respective network protocols into our software platform. That allows us to tap into the actual source of information and transport data to and from the system in realtime. The DDC (Direct Digital Control) device collects all sensor and system data into its memory, and from the DDC the needed data is drawn on request to the SmartAlert UI on the worker’s smartglasses’ display over the BACnet protocol.
From the maintenance worker’s point of view, getting the right data has to be accurate, effortless, and fast. To achieve the maximum ease-of-use we decided to use the Augumenta markers. They are simple, cost-effective, and extremely reliable in industrial environments in pinpointing data to a certain location. The marker is attached on or close to the specific equipment. The camera on the smartglasses sees and reads our markers even in half dark and from difficult angles: a worker scans the code simply “walking-by” and the most recent data is brought automatically onto the glasses.
The solution is easy not only for workers but also for developers who extend its functionality in the future. As new HVAC machines are installed, extra markers can be easily added and assigning BACnet data nodes to them can be done in a matter of minutes. The same goes for updating the existing markers and their data; editing a couple of configuration files is all it takes to reconfigure the system, and updating the software itself is not necessary.
Sometimes things don’t go as planned and outside help is needed. Augumenta solutions make this easy: a single click of a smartglasses’ button is all it takes to establish a call with a remote expert. Thanks to the camera and microphone in the glasses, experts can see what the worker is looking at on their screens, and provide accurate instructions that lead to shorter problem-solving times. The modular system also allows an expert to call more people to join the troubleshooting session when needed.
For the first deployment project in Victor Taichung’s ultramodern new factory, we chose the Google Glass EE2, water and dustproof lightweight smartglasses that are comfortable to wear even for longer periods of time. On-site integration and testing were completed in a matter of hours; a proof that Nextek’s HVAC systems and Augumenta SmartAlert are both designed with interoperability and ease of integration in mind.
“Smartglasses are the ultimate tool for realtime access to data”, says Tero Aaltonen, Augumenta Co-Founder and CEO. “Thanks to open protocols used in Nextek’s HVAC systems, we were able to integrate SmartAlert application with their system quickly and without any difficulties. The fact that the final on-site integration only took some hours and how convenient Google Glasses are for workers, demonstrate how barriers for AR adoption are truly gone.”
The first feedback has been extremely positive praising the ease-of-use of the solution and the speed of data updating at a certain data point. The information is reaching the person on the factory floor as planned.
We are pleased to announce that we will continue cooperating with Nextek and jointly target to introduce and deploy these state-of-the-art solutions for Nextek’s projects and customers. We want to continue to bring value to our customers by making data work for them. Our common goal here is to secure optimized runtime and efficient maintenance of Nextek’s systems bringing direct savings to their customers.
“HVAC is a traditional industry, but at Nextek we strive to bring in new technologies like AI and AR to create added value”, said Jin-Taung Lin, Chairman of Nextek. “Nextek is a system integration company with a focus on EPC (Engineering, Procurement and Construction), but we are not so strong in software. Working with Augumenta brings great synergies as they excel in areas we are not familiar with.”
More information about Nextek: https://en.nextekco.com/index_down.php
Real-time data is the one factor that helps you keep the machines running and optimize uptime. Getting the data from the selected KPIs at the right time helps solve issues before they turn into real trouble.
Introducing camera calibration and its importance in high-accuracy augmented reality
The eye box is the secret behind good AR UX. Discover what it is and how to take full advantage of this hidden smartglasses spec
How hundreds of millions can be saved every year by large logistics operations thanks to smartglasses and SmartMarkers.
How millions can be saved every year by introducing SmartPanel and smartglasses to reduce airframe weight, shorten idle time and shrink ground crews.