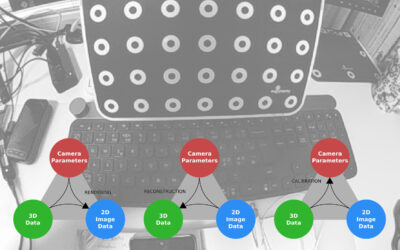
Unveiling the Magic Behind Augumenta’s AR accuracy: Camera Calibration in Smartglasses
Introducing camera calibration and its importance in high-accuracy augmented reality
Every minute of downtime is a potential revenue loss for a manufacturer, no matter what is the cause of it. Read how AR can help prevent or shorten downtimes and save money.
Downtime is as a period of time when something, a network, piece of machinery or the whole factory is not in operation. Every minute of downtime is a potential revenue loss for a manufacturer, no matter what is the cause of it. An unplanned one, resulting of a failure or a malfunction is usually the ultimate worst-case scenario, for in most cases it is far more expensive and lengthy than a scheduled maintenance break. Production lines are increasingly complicated and demands for efficiency are high in today’s manufacturing industry. Digitization initiatives; connecting people, equipment and computers, drawing and analyzing data from multiple sources, have brought new tools to minimize unexpected failures of machines in production.
Augmented reality is one of the key industry 4.0 tools to make operations more productive and it has since long been connected to predictive maintenance methods. Today, maintenance is one of the most common use cases for industrial AR. Let’s take a quick look at a few examples, how AR can help prevent or shorten those horrid downtimes and save you serious sums of money.
Unexpected breakages are expensive and harder to fix. It may be difficult to get replacing parts in a short notice, it may require an expensive expert to come and fix the equipment. Best avoid them altogether. Augmented reality is the tool to provide workers with a real-time access to critical process information and keep them informed of any troubles. With the help of AR:
In simple use, cases you can follow key values of certain equipment, like energy consumption, vibration, temperature, oil, lubricant or coolant status, conductivity data, or some other values defined critical for the process, to help identify problems before they escalate. The further you are down the digitization road and the more sources you can stream data from, the better picture you can draw of your machines, the production line or the whole plant. For example, in Hannover Messe this year, we cooperated with Connected Production to demonstrate the power of AR and Industry 4.0 platform together. With an IoT platform in the background, streaming data from MES, we could bring real-time production data such as energy consumption and alerts to a smartglasses’ display and ensure problems were caught before they even were problems.
In machine maintenance, be it scheduled or unplanned, it is the number one priority to keep any break as short as possible. There are several proven use cases for AR in maintenance supporting this target. Smartglasses leave your hands free to focus on the task, not checking paper lists, manuals or flipping through instructions on a tablet. So, if a failure already took place, here’s how AR can help minimize the damages:
Finally, let’s throw here some numbers about the costs. This Business Insider graphic shows how expensive unexpected downtime can be: in automotive industry a minute of unplanned downtime can cost $22 000. These numbers are not new but still very valid.
Another study on British manufacturers reported last year that on average 3% of all working days are lost annually in manufacturing due to faulty machinery, equating to 49 hours of work and £31,000 per company. According to the UK manufacturers in the study, 53% of machinery downtime is caused by hidden internal faults. Similar numbers are referred to with US manufacturers in another article: unplanned downtime costs industrial manufacturers an estimated $50 billion annually. Equipment failure is the cause of 42 % of this unplanned downtime.
In the light of these numbers, AR has a huge potential in helping improve the bottom line by helping minimize downtime. You can start with industrial AR no matter where in the digitization continuum you are in. In a fully digitized smart factory it is a short step to take. If you’re not there yet, start small. Define the critical process and equipment in your factory and the key data points and start deploying AR to secure an efficient uptime of your production lines.
If you’d like to know more about how to get started, have a look at this checklist. We’re happy to help you on the way.
Introducing camera calibration and its importance in high-accuracy augmented reality
The eye box is the secret behind good AR UX. Discover what it is and how to take full advantage of this hidden smartglasses spec
How hundreds of millions can be saved every year by large logistics operations thanks to smartglasses and SmartMarkers.
How millions can be saved every year by introducing SmartPanel and smartglasses to reduce airframe weight, shorten idle time and shrink ground crews.